Резец является одним из самых распространенных металлорежущих инструментов. Он широко применяется для выполнения резьбы, обработки плоскостей, цилиндрических и фасонных поверхностей, а также при строгальных и долбежных работах. Из статьи Вы узнаете важную и профессиональную информацию о применении подрезных, отрезных, расточных, фасочных и фасонных резцов; их геометрических параметрах и этапах заточки в простом и понятном изложении.
-
Резец является одним из самых распространенных металлорежущих инструментов. Он широко применяется для выполнения резьбы, обработки плоскостей, цилиндрических и фасонных поверхностей, а также при строгальных и долбежных работах.
-
-
Резец состоит из рабочей части, называемой головкой, и тела — державки. Основными элементами рабочей части являются главная режущая кромка, вспомогательная режущая кромка и вершина — точка пересечения двух кромок. Срезание слоя металла осуществляется главной кромкой, имеющей прямую или фасонную форму. Образующаяся в процессе работы стружка сходит по передней поверхности резца.
-
-
Державка служит для закрепления инструмента в держателе станка и обычно имеет квадратную или прямоугольную форму поперечного сечения.
-
-
В зависимости от того, как по отношению к обрабатываемой поверхности установлены резцы, эти инструменты подразделяются на радиальные и тангенциальные резцы. Первые расположены перпендикулярно оси детали, вторые — касательно.
-
-
Если первый тип резца имеет широкое применение в промышленности за счет простоты своего крепления и более удобного выбора геометрических параметров режущей части, то второй используется главным образом на токарных автоматах и полуавтоматах, где особенно важна чистота обработки.
-
-
По направлению подачи резцы подразделяются на два типа: правые и левые. Если при наложении ладони правой руки сверху на инструмент главная режущая кромка находится под большим пальцем, то резец называется правым. Если режущая кромка располагается подобным образом при наложении левой руки, то и резец, соответственно, будет левым.
-
-
Форма головки и её положение относительно стержня также могут быть различными. По этим параметрам резцы делятся на прямые, отогнутые, изогнутые и с оттянутой головкой.
-
-
-
Прямые резцы имеют прямую ось в плане и боковом виде. Ось отогнутых в плане изогнута. У изогнутых ось загнута в боковом виде. У резцов с оттянутой головкой ширина головки меньше ширины тела резца.
-
-
Резцы применяются для токарных, строгальных и долбежных работ и имеют соответствующие названия. Сейчас мы более подробно коснемся резцов, используемых на токарных станках, и расскажем об их разновидностях.
Токарные резцы
Геометрические параметры токарных резцов
-
-
Токарные резцы подразделяются на проходные, подрезные, отрезные, расточные, фасочные и фасонные.
-
-
Подрезные токарные резцы служат для подрезания уступов под прямым или острым углом к основному направлению обтачивания. Обычно этот инструмент имеет поперечную подачу.
-
Отрезные резцы предназначены для отрезания материала от прутков небольшого диаметра. Как правило, для этих целей применяются инструмент с оттянутой головкой. В связи с тем, что работа ведется с большим усилием, а отвод стружки из зоны резания затруднен, нередко происходят выкрашивание или сколы режущей части инструмента, а иногда и отрыв пластинки от державки.
-
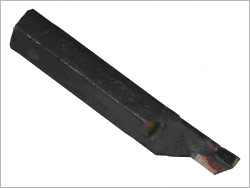
-
Расточные резцы необходимы для обработки отверстий. Они имеют меньшие поперечные размеры, чем обрабатываемое отверстие, и довольно большую длину. В силу своей малой жесткости, расточные резцы не позволяют снимать стружку большого сечения.
-
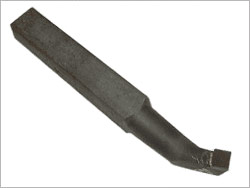
-
Для обработки длинных отверстий или отверстий большого диаметра применяются вставные резцы круглого или квадратного сечения, используемые вместе с державками. Державки позволяют производить расточку с помощью как одностороннего, так и двустороннего резца.
-
-
Фасочные резцы предназначены для снятия наружных и внутренних фасок.
-
-
Фасонные резцы используются для получения детали сложной формы.
-
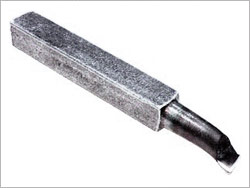
-
-
-
-
При выборе токарного резца следует учитывать целый ряд требований, обеспечивающих высокую производительность и точность обработки. Это
-
-
- материал режущей части резца;
-
-
- геометрия режущей части;
-
-
прочность и виброустойчивость державки и режущих кромок;
-
-
- форма и размеры пластинки инструментального материала;
-
-
- способ и конструкция крепления пластинки инструментального материала (если используются пластины с механическим креплением);
-
-
- способ стружколомания;
-
-
- размеры, шероховатость, геометрия и конструкция гнезда для крепления пластины инструментального материала.
-
-
Все перечисленные факторы определяют выбор оптимальных режимов резания – глубины, подачи и скорости.
-
-
-
Главными критериями выбора геометрических параметров резца являются:
-
-
- стойкость инструмента (время образования на его задней или передней поверхности допустимой величины площадки износа);
-
-
-
- размерная стойкость инструмента (допустимое изменение его настроечного размера);
-
-
- поддержание заданной шероховатости обработанной поверхности;
-
-
уменьшение амплитуды автоколебаний в ходе рабочего процесса.
-
-
-
При выборе резца следует учитывать такие параметры, как его углы. Они измеряются в секущих плоскостях и обозначаются греческими буквами.
-
-
К основным углам относятся главный задний угол, передний угол, угол заострения и угол резания. Все они находятся в главной секущей плоскости — перпендикулярной главной режущей кромке и основной плоскости.
-
-
Главным задним углом (его принято обозначать буквой «альфа») называется угол между главной задней поверхностью резца и плоскостью резания. Его назначение — уменьшение трения задней поверхности резца о заготовку. Увеличение заднего угла вызывает уменьшение угла заострения, что влечет за собой снижение прочности лезвия и увеличение шероховатости обрабатываемой поверхности. Уменьшение заднего угла, в свою очередь, повышает трение, что ускоряет износ резца и снижает качество обработки.
-
-
При обработке твёрдых материалов величины задних углов снижаются, а при работе с более мягкими — увеличиваются. Рекомендуемые значения главного заднего угла зависят от типа резца и указываются в таблицах.
-
-
Угол между передней и главной задней поверхностями резца (обозначается буквой «бетта») называется углом заострения.
-
-
Передний угол («гамма») - это угол между передней поверхностью резца и плоскостью, проведенной через главную режущую кромку перпендикулярно к плоскости резания.
-
-
Назначение переднего угла - уменьшить деформацию срезаемого слоя и облегчить сход стружки. Увеличение угла облегчает процесс резания и позволяет снизить усилие подачи резца, но прочность режущего клина снижается. Отклонение величины переднего угла всего на 5 градусов от рекомендуемых оптимальных значений может вызвать снижение стойкости резцов почти в три раза. Уменьшение переднего угла повышает стойкость резцов.
-
-
И наконец, угол резания («дельта») - угол между передней поверхностью резца и плоскостью резания.
-
-
Кроме того, существуют вспомогательный задний угол, главный угол в плане, вспомогательный угол в плане, угол при вершине резца и угол наклона главной режущей кромки.
-
-
Вспомогательным задним углом называется угол между вспомогательной задней поверхностью и плоскостью, проходящей через вспомогательную режущую кромку перпендикулярно к основной плоскости. Этот угол измеряется на вспомогательной секущей плоскости, перпендикулярной к вспомогательной режущей кромке и основной плоскости. Аналогично главному заднему углу он обозначается как «альфа1».
-
-
Угол между главной режущей кромкой и направлением подачи называется главным углом в плане и обозначается буквой «фи». Его назначение – изменять соотношение между шириной и толщиной среза при постоянных глубине резания и подаче. При уменьшении угла повышается прочность вершины резца, но силу приложения приходится увеличивать. При этом повышается трение об обрабатываемую поверхность и возникают вибрации.
-
Выбор величины главного угла в плане зависит от условий обработки,, конструкции резцов и особенностей крепления пластин. Значение угла «фи» может быть 90, 75, 63, 60, 50, 45, 35, 30, 20, 10 градусов, что позволяет подобрать угол , наиболее соответствующий конкретным условиям.
-
-
Резцы с малыми углами от 10 до 20 градусов применяются при обработке массивных деталей на тяжелых станках. Нежесткие изделия обрабатывают под углами 60-75 градусов, а угол 90 градусов применяется при наличии на заготовке ступеней с торцами.
-
-
Вспомогательным углом в плане называется угол между вспомогательной режущей кромкой и направлением подачи (по аналогии обозначается «фи1»). Уменьшение угла снижает шероховатость обработанной поверхности.
-
-
Угол, образованный пересечением главной и вспомогательной режущих кромок, называется углом при вершине. Его значение обозначается буквой «эпсилон».
-
-
Главная режущая кромка резца может иметь различные углы наклона с линией, проведенной через вершину резца параллельно основной плоскости.
-
-
Угол наклона режущей кромки обозначается буквой «ламбда». Изменение этого угла позволяет управлять направлением схода стружки и условиями контакта резца с заготовкой. Значения 12-15 градусов следует применять при черновой обработке и прерывистом резании с ударами. При точении закаленной стали значение «ламбды» следует принять от 25 до 35 градусов. При чистовой обработке детали используются резцы, угол наклона режущей кромки которых меньше или равен нулю.
Заточка резцов
-
Заточка токарных резцов производится как при их изготовлении, так и при износе. Процесс заточки проходит на точильно-шлифовальных станках с непрерывным охлаждением. Сначала затачивается главная поверхность, затем задняя и вспомогательная. После этого обрабатывают переднюю поверхность резца до получения ровной режущей кромки.
-
-
На каждом станке для заточки резцов имеется два шлифовальных круга: из электрокорунда и из зеленого карбида кремния. Первый применяется для обработки резцов из быстрорежущей стали, второй используется для заточки твердосплавных резцов. Для проверки правильности заточки резца существуют специальные шаблоны.
-
-
Статья предоставлена компанией Кибер – интернет-магазин инструментов.
КОНТАКТЫ КОМПАНИИ
|